Moulage et usinage
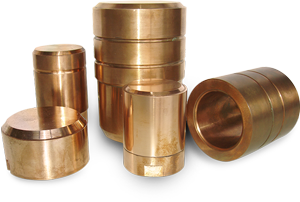
Le procédé de moulage sous pression en zamak prévoit l’injection de métal en fusion directement dans un moule, celle-ci est adaptée pour des formes géométrique complexe et précise, aucun procédé industriel ne peut atteindre le résultat que donne la fonderie sous pression par injection.
Cette technique de l’alliage zamak, dont les principaux composants sont le zinc et l’aluminium est utilisée dans différentes applications industrielles.
Les produits fabriqués sont des accessoires, des composants et des petites pièces de différentes natures pour alléger et remplir sa mission de résistance mécanique élevée.
Ce procédé à haute pression donne aux pièces une structure de surface dense et à grain fin, avec un large éventail de propriétés physiques et mécaniques, telle la résistance à la fatigue qui est un critère important dans le choix du métal. En effet, la rupture due à la fatigue est le cas le plus fréquent dans les pièces mécaniques. Le Zamak a une résistance à la fatigue 7 à 10 fois plus importante qu’un plastique de type ABS.
L’un des procédés les plus utilisés est le moulage sous pression de l’aluminium, d’autres métaux sont également utilisés comme le laiton, le magnésium et les alliages de zinc selon le cahier des charges.
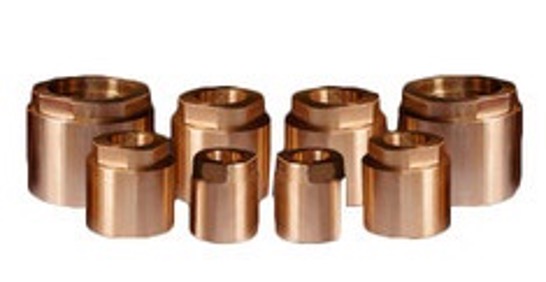
Les différents types de moulage sous pression
La fonderie de moulages sous pression est une technique, connue aussi sous le nom de coulée sous pression et mise au point aux États-Unis au XIXe siècle, peut notamment être de deux types :
* à chambre chaude
* à chambre froide
Le premier procédé est en général utilisé pour le travail du zamak et recourt à un four de fusion : il permet ainsi un contrôle optimal de la température, avec le prélèvement du métal en fusion directement dans le réservoir, en optimisant les temps de fabrication.
La pression ne dépasse pas 140 BARS, pour une finition de haute qualité de la surface de l’alliage.
Le choix est guidé par une production rapide et en grande série
Ce process de fonderie permet de produire à haute cadence. Grâce aux moules d’injection en acier trempé, le procédé peut être répété plusieurs centaines de milliers de fois pour créer des pièces métalliques parfaitement identiques. Avec les alliages de zinc, les cadences de production sur machines conventionnelles à chambre chaude sont élevées et peuvent dans certains cas dépasser mille injections par heure pour des pièces minces et de faibles dimensions.
La fonderie sous pression est donc parfaitement appropriée pour la production en grande série. De plus, elle nécessite que peu ou pas d’usinage.
Des moules durables et précis
Les outillages sont solides, ils résistent longtemps à l’usure, également résistants à la chaleur, présentent une bonne stabilité dimensionnelle tout en conservant des tolérances étroites.
En fonction de la complexité de la pièce, la grande précision des outillages permet d’éliminer un maximum d’opérations d’usinage.
L’alliage Zamak a une durée de vie des outillages plus longue, ce qui aide à réduire les coûts de production.
Finitions
Plusieurs procédés de finition peuvent être appliqués sur les pièces de fonderie brutes. Tout d’abord, pour la préparation des états de surfaces, il y a le grenaillage qui est une projection de particules métalliques sur les pièces en vue de supprimer les bavures et traces de moulage. Il y a ensuite le sablage qui est la projection de sable ou de petites billes de verre sur la pièce à l’aide d’un jet dirigé. La tribofinition : les pièces sont placées dans un bac vibrant qui contient des cailloux abrasifs en céramique. L’émerisage et l’ébavurage permettent la suppression manuelle des traces généralement sur des pièces de grandes dimensions et/ou en faible nombre, et enfin il y a le polissage, qui est fait préalablement à un traitement de surface de très haute qualité d’aspect, permettant la préparation pour un chrome brillant ou une belle dorure.
Assemblage
Pour supprimer les opérations d’usinage (perçage, filetage et taraudage) et les éléments d’assemblage (vis, écrous, rivets), la fonderie sous pression donne la possibilité de réaliser des liaisons comme le sertissage, le rivetage, le vissage, l’emmanchement, le collage ou encore l’insert surmoulé. Le Zamak est parfaitement adapté à ce type de liaisons.ration pour un chrome brillant ou une belle dorure.
En conclusion
Depuis l’invention du premier équipement de fonderie sous pression en 1839, le procédé de moulage sous pression a montré ses avantages à différents usages industriels, mécaniques et semble encore avoir de beaux jours.
Avec les exigences d’écoconception que requièrent aujourd’hui les industries mondiales, la fonderie sous pression reste un modèle de développement durable, du fait de sa consommation basse en énergie et le recyclage du zinc, principal constituant du Zamak. En plus, la transformation et la valorisation des fonderies de zinc se fait sur le territoire national (Genlis Metal), par conséquent, il n’y a pas de problème d’approvisionnement, ni de dépendance vis-à-vis d’un pays tiers et donc une empreinte carbone réduite pour le transport.
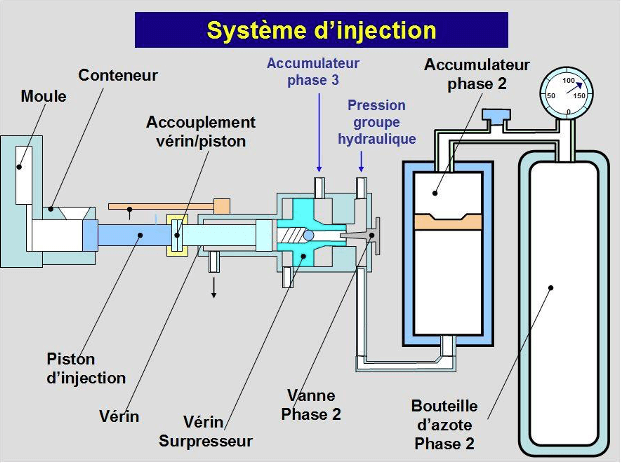
Les outillages sont solides, ils résistent longtemps à l’usure, également résistants à la chaleur, présentent une bonne stabilité dimensionnelle tout en conservant des tolérances étroites.
En fonction de la complexité de la pièce, la grande précision des outillages permet d’éliminer un maximum d’opérations d’usinage.
L’alliage Zamak a une durée de vie des outillages plus longue, ce qui aide à réduire les coûts de production.
Les paramètres de fabrication
Sur les machines traditionnelles, on décompose l’injection en 3 phases. La première phase, à vitesse lente permet d’amener le métal jusqu’à l’attaque de coulée. La deuxième phase à vitesse rapide permet de remplir l’empreinte. Enfin, la troisième phase se déclenche après le remplissage et est une phase de compression à très forte pression qui permet de combler le retrait du métal pendant la solidification et de comprimer fortement les porosités (soufflures, retassures) dans la pièce. Sur les machines récentes, jusqu’à une vingtaine de phases peuvent être programmées si besoin pour piloter plus finement l’injection avec des variations de vitesse du piston au cours du remplissage et des évolutions de pression pendant la phase de compression ou enfin un freinage du piston en fin de remplissage.
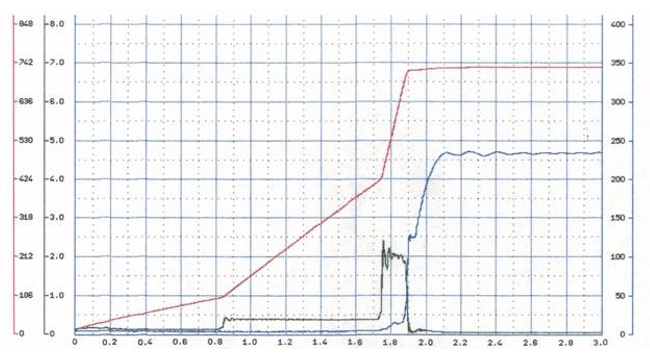
Ecrit par Philippe Herrmann, gérant de DELTA METAL basée à Munster en Alsace Haut-Rhin.
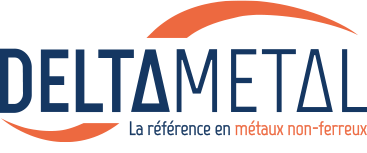