TECHNIQUES D’ÉLABORATION
La métallurgie moderne repose sur des techniques d’élaboration sophistiquées permettant de créer des produits aux propriétés spécifiques.
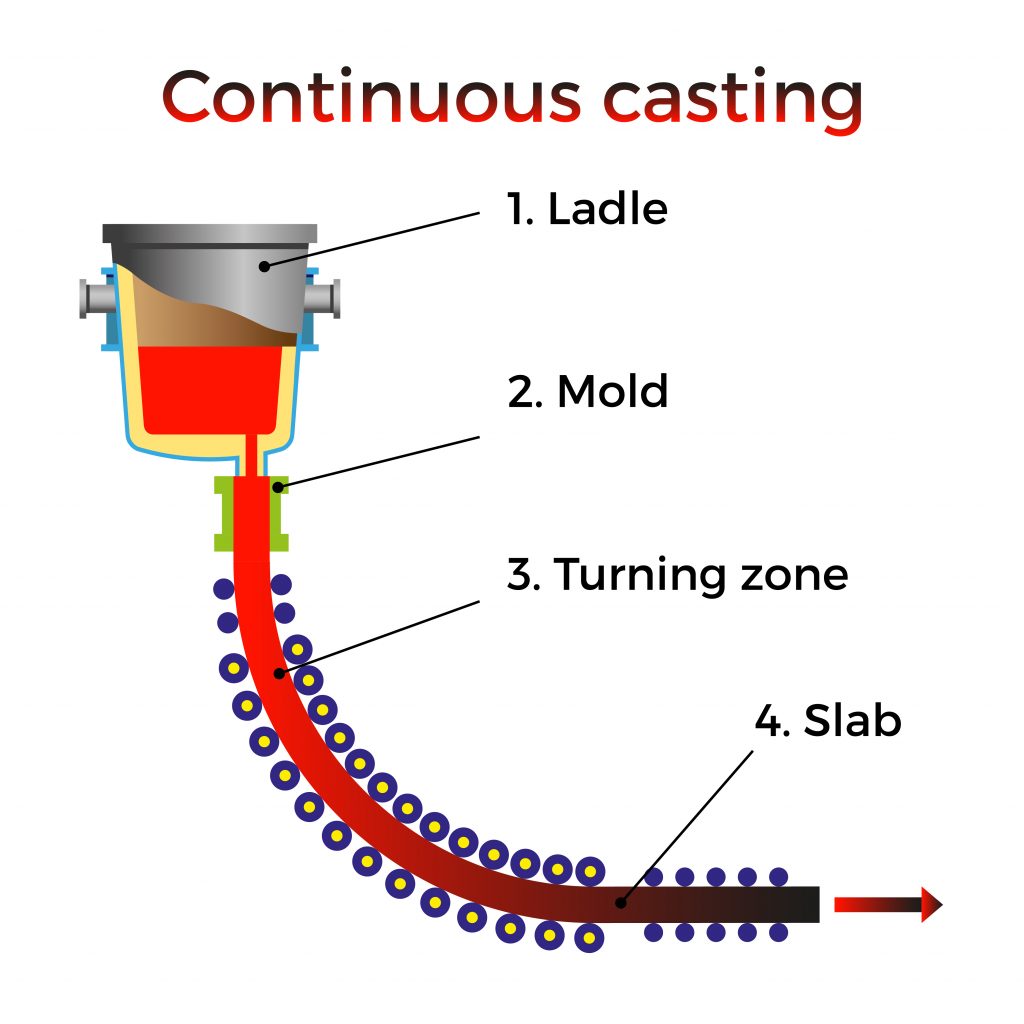
COULÉE CONTINUE
La coulée continue est un procédé de solidification du métal en fusion. Il consiste à remplir un moule de métal liquide puis à en extraire lentement le produit.
L’extraction du produit solidifié est compensée par un apport de métal liquide chaud : le métal liquide entre d’un côté du moule pendant que de l’autre côté en sort un produit solide.
Ce procédé permet d’obtenir des demi-produits de bel aspect, facilement usinables, avec des côtes précises et de bonnes caractéristiques mécaniques.
CENTRIFUGÉ
La coulée par centrifugation est un procédé qui utilise la force centrifuge appliquée au métal liquide coulé dans une coquille métallique ou sable. Le métal liquide est soumis à une force centrifuge tendant à l’éloigner de l’axe de rotation et à le plaquer à la paroi de la coquille.
Il existe 3 types de centrifugation : horizontal, vertical et oblique.
Ce procédé permet d’obtenir des produits cylindriques creux, présentant de très bonnes qualités physiques et mécaniques.
ETIRÉ
L’élaboration consiste à mettre en forme un profilé par allongement et réduction de section en lui faisant subir une traction à travers une filière. Ce processus permet d’étirer la barre afin d’obtenir des tolérances dimensionnelles serrées. Le durcissement (écrouissage) qui s’en suit modifie les caractéristiques mécaniques en augmentant leur résistance et leur rigidité.
EXTRUDÉ
Procédé de fabrication de certains matériaux type tubes, plaques, profilés, selon lequel la matière est compressée et contrainte de traverser une filière ayant la forme de la pièce à obtenir. De plus, les pièces présentent des états de surface excellents, ce qui permet souvent de les utiliser sans usinage complémentaire.
LAMINÉ
Le laminage est un procédé de fabrication par déformation plastique obtenue par compression continue au passage entre deux cylindres contrarotatifs appelés laminoir.
En raison de ce mouvement de rotation et de la compression générée par les cylindres, il se produit une réduction en continu de l’épaisseur initiale. Suivant les profils à réaliser le métal chauffé va passer dans une série de plusieurs laminoirs. Il faut distinguer le laminage à chaud (800 – 1200 °C) pour les grandes épaisseurs, du laminage à froid (T < 200 °C) pour les épaisseurs inférieures à 6MM.
Le laminage à chaud permet d’améliorer les caractéristiques mécaniques dans le sens de l’étirement (sens de laminage). C’est lors du laminage à froid que le métal voit ses caractéristiques mécaniques changer, en effet l’écrouissage local (déformation plastique) augmente la zone de déformation élastique. La résistance élastique est repoussée, mais la résistance à la rupture est constante (il s’agit d’une propriété interne du matériau).
FORGÉ
Le forgeage permet de passer d’une forme brute (lingot, barre) à une forme plus évoluée, par martelage de la pièce, en exploitant la plasticité (déformation) du matériau.
Le forgeage est la déformation du métal à chaud ou à froid entre deux outils plats par martelage ou par pression à l’aide d’une presse de forge ou d’une machine à forger. Il permet, par déformation appropriée, d’obtenir des produits ou demi-produits à la forme désirée : bloc, tôle, barre, fil, profilé…
Les pièces obtenues sont plus résistantes aux contraintes mécaniques. Il provoque un resserrement du métal et une orientation des cristaux par l’action d’un travail de déformation dans une ou plusieurs directions privilégiées.
FRITTÉ
Le frittage est un procédé de fabrication de pièces consistant à chauffer une poudre sans la mener jusqu’à la fusion. Sous l’effet de la chaleur, les grains se soudent entre eux, ce qui forme la cohésion de la pièce.
Le frittage est réalisé dans un four à haute température (proche de la température de fusion du matériau) sous atmosphère contrôlée ou sous vide. Pour donner quelques gammes de température, le frittage du tungstène s’effectue aux alentours de 2000 à 3050°C et celui du molybdène autour de 1800 à 2300°C.
Le frittage permet d’obtenir des formes complexes à partir de l’outillage de compactage, sans nécessiter d’opérations d’usinage supplémentaires grâce à sa grande précision dimensionnelle. Les tolérances peuvent être améliorées par des opérations d’usinage. L’état de surface est de meilleure qualité que celui des matières solides usinées.