Fundición y mecanizado
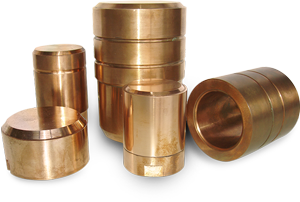
El proceso de fundición a presión de zamak implica la inyección de metal fundido directamente en un molde, esto es adecuado para formas geométricas complejas y precisas, ningún proceso industrial puede lograr el resultado que da la fundición a presión por inyección.
Esta técnica de aleación de zamak, cuyos componentes principales son el zinc y el aluminio, se utiliza en diferentes aplicaciones industriales.
Los productos fabricados son accesorios, componentes y pequeñas piezas de distintos tipos para aligerar y cumplir su misión de alta resistencia mecánica.
Este proceso de alta presión confiere a las piezas una estructura superficial densa y de grano fino, con una amplia gama de propiedades físicas y mecánicas, como la resistencia a la fatiga, que es un criterio importante en la elección del metal. De hecho, el fallo por fatiga es el caso más común en piezas mecánicas. El zamak tiene una resistencia a la fatiga de 7 a 10 veces mayor que el plástico tipo ABS.
Uno de los procesos más utilizados es la fundición a presión de aluminio, también se utilizan otros metales como latón, magnesio y aleaciones de zinc según las especificaciones.
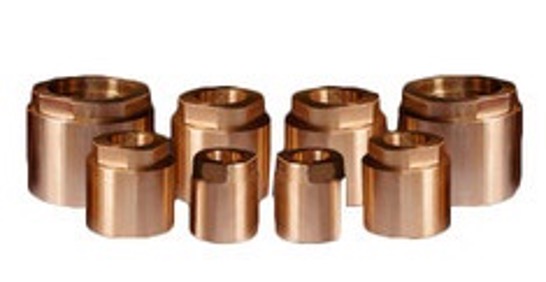
Los diferentes tipos de fundición a presión.
La fundición a presión es una técnica, también conocida como die casting y desarrollada en Estados Unidos en el siglo XIX, que puede ser de dos tipos:
* en habitación caliente
* en cámara frigorífica
El primer proceso se utiliza generalmente para trabajar el zamak y utiliza un horno de fusión: permite así un control óptimo de la temperatura, con retirada del metal fundido directamente del depósito, optimizando los tiempos de fabricación.
La presión no supera los 140 BARES, para un acabado de alta calidad de la superficie de la aleación.
La elección se basa en una producción rápida y a gran escala.
Este proceso de fundición permite una producción a altos ritmos. Gracias a los moldes de inyección de acero endurecido, el proceso se puede repetir varios cientos de miles de veces para crear piezas metálicas perfectamente idénticas. En el caso de las aleaciones de zinc, las velocidades de producción en las máquinas de cámara caliente convencionales son elevadas y, en algunos casos, pueden superar las mil inyecciones por hora para piezas finas y pequeñas.
Por lo tanto, la fundición a presión es ideal para la producción en grandes series. Además, requiere poco o ningún mecanizado.
Moldes duraderos y precisos
Las herramientas son sólidas, resisten el desgaste durante mucho tiempo, también son resistentes al calor, tienen buena estabilidad dimensional y mantienen tolerancias estrechas.
Dependiendo de la complejidad de la pieza, la alta precisión de las herramientas permite eliminar el mayor número posible de operaciones de mecanizado.
La aleación de Zamak tiene una vida útil más larga, lo que ayuda a reducir los costos de producción.
Acabados
Se pueden aplicar varios procesos de acabado a las piezas fundidas en bruto. En primer lugar, para la preparación de las condiciones superficiales se utiliza el granallado, que es una proyección de partículas metálicas sobre las piezas para eliminar rebabas y restos de moldeo. Luego está el arenado, que es la proyección de arena o pequeñas perlas de vidrio sobre la pieza mediante un chorro dirigido. Triboacabado: las piezas se colocan en un tanque vibratorio que contiene piedras abrasivas cerámicas. El rectificado y desbarbado permiten la eliminación manual de marcas generalmente en piezas grandes y/o pocas, y finalmente está el pulido, que se realiza antes de un tratamiento superficial de muy alta calidad, permitiendo la preparación para un cromado brillante o un hermoso dorado.
Ensamblaje
Para eliminar operaciones de mecanizado (taladrado, roscado y roscado) y de elementos de montaje (tornillos, tuercas, remaches), la fundición a presión da la posibilidad de realizar conexiones como engarzado, remachado, atornillado, etc., encajando, pegando o incluso el inserto sobremoldeado. El zamak se adapta perfectamente a este tipo de conexión para obtener un cromo brillante o un dorado bonito.
En conclusión
Desde la invención del primer equipo de fundición a presión en 1839, el proceso de fundición a presión ha demostrado sus ventajas para diferentes usos industriales y mecánicos y todavía parece pasar un buen momento.
Con las exigencias de ecodiseño que exigen hoy las industrias globales, la fundición a presión sigue siendo un modelo de desarrollo sostenible, debido a su bajo consumo energético y al reciclaje del zinc, principal constituyente del Zamak.. Además, en el territorio nacional se realiza la transformación y valorización de fundiciones de zinc (Metal Genlis), por lo tanto, no hay problema de suministro, ni dependencia de un tercer país y por tanto una huella de carbono reducida para el transporte.
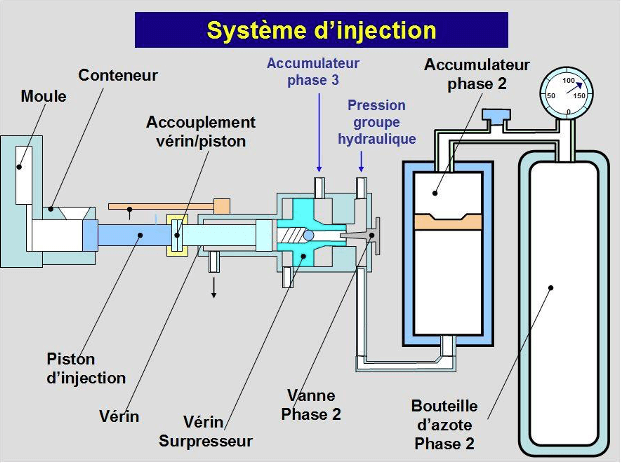
Las herramientas son sólidas, resisten el desgaste durante mucho tiempo, también son resistentes al calor, tienen buena estabilidad dimensional y mantienen tolerancias estrechas.
Dependiendo de la complejidad de la pieza, la alta precisión de las herramientas permite eliminar el mayor número posible de operaciones de mecanizado.
La aleación de Zamak tiene una vida útil más larga, lo que ayuda a reducir los costos de producción.
Parámetros de fabricación
En las máquinas tradicionales, la inyección se divide en 3 fases. La primera fase, a baja velocidad, permite llevar el metal a la etapa de fundición. La segunda fase a alta velocidad llena la impresión. Finalmente, la tercera fase se activa después del llenado y es una fase de compresión a muy alta presión que permite compensar la contracción del metal durante la solidificación y comprimir fuertemente las porosidades (golpes, hundimientos) de la pieza. En las máquinas recientes, se pueden programar hasta veinte fases si es necesario para controlar con mayor precisión la inyección con variaciones de velocidad del pistón durante el llenado y cambios de presión durante la fase de compresión o finalmente frenado del pistón al final del llenado.
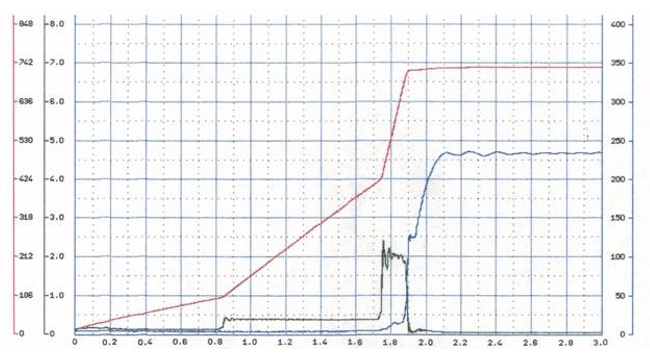
Escrito por Philippe Herrmann, director de DELTA METAL con sede en Munster, Alsacia-Alto Rin.
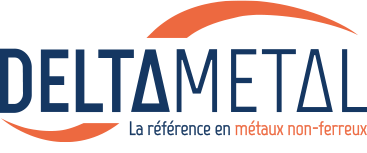